Manufacturing Resource Planning In Modern ERP: Complete Guide, Features and Details
In today’s fast-paced manufacturing landscape, staying competitive requires more than just producing quality products. It demands efficient resource management, streamlined processes, and accurate forecasting. This is where Manufacturing Resource Planning (MRP) comes in, and when integrated into a modern Enterprise Resource Planning (ERP) system, it becomes a powerhouse for optimizing your entire manufacturing operation. I’ve seen firsthand how transformative a well-implemented ERP with robust MRP capabilities can be, moving companies from reactive firefighting to proactive planning and significant cost savings.
Think of MRP as the brain of your manufacturing process. It takes your sales forecasts, production schedules, and inventory levels and translates them into detailed plans for material procurement, machine utilization, and labor allocation. When coupled with ERP, it’s no longer a standalone function but becomes seamlessly integrated with finance, sales, supply chain, and other crucial departments. This integration eliminates data silos, improves communication, and provides a holistic view of your business.
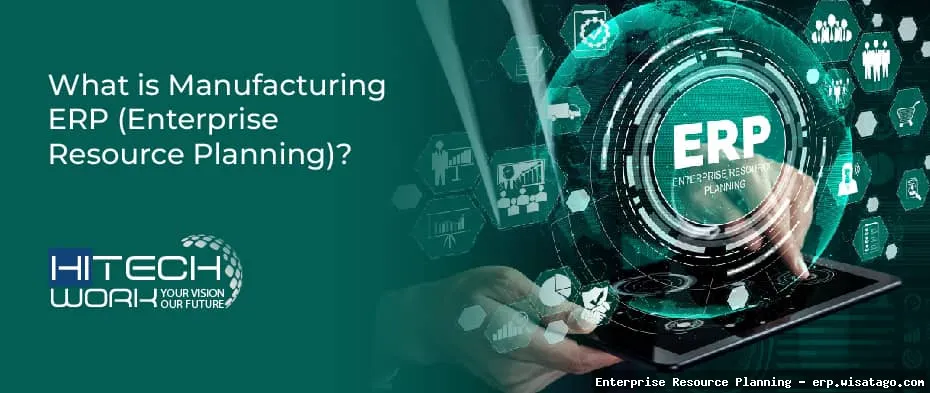
This article will delve into the world of MRP within modern ERP systems. We’ll explore its core functionalities, benefits, implementation considerations, and how to choose the right solution for your specific needs. Whether you’re a small manufacturer looking to upgrade from spreadsheets or a large enterprise seeking to optimize your existing ERP, this guide will provide valuable insights to help you navigate the complexities of MRP and unlock its full potential.
Manufacturing Resource Planning In Modern ERP: Complete Guide, Features and Details
Manufacturing Resource Planning (MRP) is a planning and control system for manufacturing. It evolved from Material Requirements Planning (MRP) and aims to coordinate all resources used in manufacturing, from raw materials to finished goods. In modern ERP systems, MRP is not a separate module but an integral part of a unified platform, allowing for real-time data sharing and collaboration across departments.
Understanding the Evolution: From MRP to MRP II to Modern ERP
The journey from Material Requirements Planning (MRP) to Manufacturing Resource Planning (MRP II) and finally its integration into modern ERP systems represents a significant evolution in manufacturing management. MRP focused primarily on material planning, answering the question: “What materials do we need, and when?” MRP II expanded this scope to include capacity planning, workforce scheduling, and financial planning, aiming to synchronize all aspects of manufacturing. Modern ERP takes it a step further by integrating MRP II with other business functions like finance, sales, CRM, and supply chain management, creating a unified system that provides a comprehensive view of the entire enterprise. This evolution reflects the increasing complexity of modern manufacturing and the need for integrated solutions to manage it effectively. Think of it as moving from managing individual ingredients to baking a whole cake – you need to consider all the elements and how they interact to achieve the desired result.
Core Functionalities of MRP in ERP
MRP within an ERP system encompasses a wide range of functionalities designed to optimize manufacturing processes. These include:
- Demand Forecasting: Analyzing historical data and market trends to predict future demand for products. This is crucial for accurate production planning. I’ve seen companies drastically reduce inventory costs by implementing robust demand forecasting models within their ERP.
- Bill of Materials (BOM) Management: Maintaining a detailed list of all components, assemblies, and raw materials required to manufacture a product. Accurate BOMs are essential for precise material planning.
- Inventory Management: Tracking inventory levels in real-time, optimizing stock levels, and minimizing carrying costs. Features like cycle counting and ABC analysis are often included.
- Production Planning: Creating production schedules based on demand forecasts, available capacity, and material availability. This ensures timely production and efficient resource utilization.
- Capacity Planning: Assessing the availability of resources (machines, labor) to meet production demands. This helps identify bottlenecks and optimize resource allocation.
- Material Requirements Planning: Calculating the quantity of raw materials and components needed to meet production schedules, taking into account lead times and inventory levels.
- Shop Floor Control: Monitoring and controlling production activities on the shop floor, including tracking work orders, managing labor, and capturing production data.
- Purchasing: Generating purchase orders for raw materials and components based on material requirements. Integration with supplier portals streamlines the procurement process.
Benefits of Integrating MRP with ERP
The integration of MRP with ERP offers numerous advantages over using standalone systems. These benefits can significantly impact a company’s bottom line and overall competitiveness.
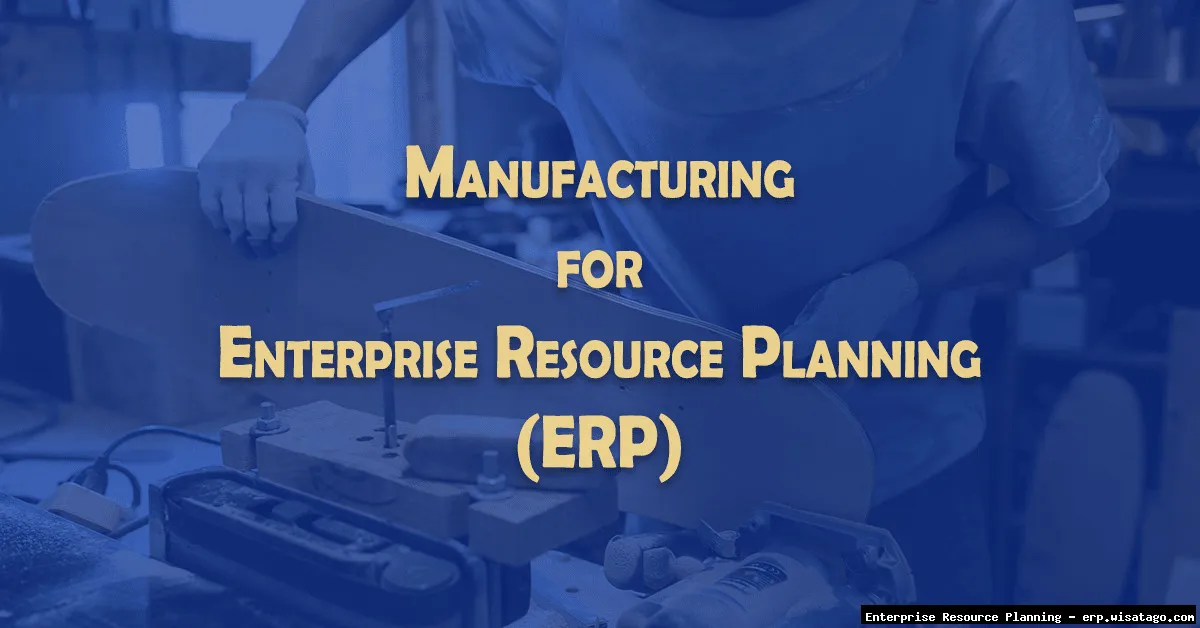
Enhanced Visibility and Collaboration
One of the most significant benefits is improved visibility across the entire organization. With all data centralized in a single ERP system, departments can access real-time information about inventory levels, production schedules, sales orders, and financial performance. This enhanced visibility facilitates better communication and collaboration between departments, leading to faster decision-making and improved efficiency. For example, the sales team can instantly check inventory availability before committing to an order, and the production team can adjust schedules based on real-time demand changes.
Improved Inventory Management
MRP integrated with ERP allows for more accurate inventory management. By tracking inventory levels in real-time and using demand forecasting, companies can optimize stock levels, reduce carrying costs, and minimize the risk of stockouts. Features like automated reorder points and safety stock calculations help ensure that the right materials are available at the right time. I’ve witnessed companies reduce their inventory holding costs by as much as 20% after implementing an ERP system with strong MRP capabilities.
Streamlined Production Processes
The integration of MRP and ERP streamlines production processes by automating tasks, reducing manual data entry, and improving communication between departments. Production schedules can be automatically generated based on demand forecasts and material availability, and shop floor control features allow for real-time monitoring of production activities. This leads to increased efficiency, reduced lead times, and improved on-time delivery performance.
Accurate Costing and Profitability Analysis
ERP systems with integrated MRP provide accurate costing information by tracking all costs associated with production, including raw materials, labor, and overhead. This allows companies to accurately calculate the cost of goods sold (COGS) and perform profitability analysis at the product level. This information is crucial for making informed decisions about pricing, product mix, and resource allocation.
Better Decision-Making
With access to real-time data and comprehensive reporting capabilities, managers can make better-informed decisions about all aspects of the manufacturing operation. This includes decisions about production planning, capacity planning, inventory management, and resource allocation. The ability to analyze data and identify trends allows companies to proactively address challenges and capitalize on opportunities.
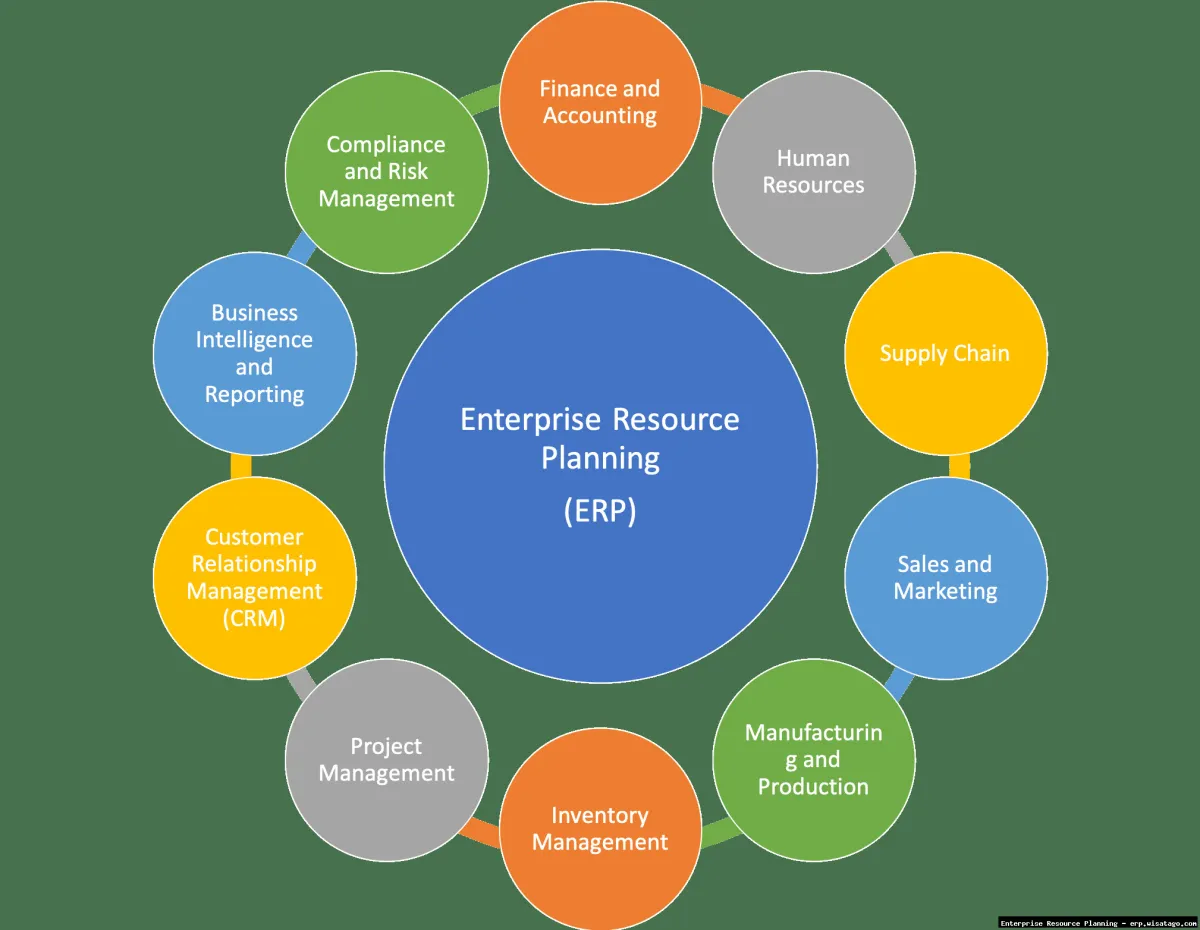
Key Considerations for Implementing MRP in ERP
Implementing MRP within an ERP system is a complex project that requires careful planning and execution. Here are some key considerations to ensure a successful implementation:
Data Accuracy and Cleansing
Accurate data is critical for the success of any MRP implementation. Before implementing the system, it’s essential to cleanse and validate existing data, including BOMs, inventory records, and customer orders. Inaccurate data can lead to incorrect production plans, material shortages, and ultimately, project failure. I’ve seen projects delayed for months due to poor data quality. Invest time in data cleansing upfront to avoid costly problems later.
Process Standardization
ERP implementation provides an opportunity to standardize processes across the organization. This involves documenting existing processes, identifying areas for improvement, and designing new processes that align with the ERP system’s capabilities. Standardized processes ensure consistency, reduce errors, and improve efficiency. Resistance to change is common, so it’s important to involve employees in the process design and provide adequate training.
User Training and Adoption
Proper user training is essential for successful ERP adoption. Users need to understand how to use the system effectively and how it impacts their daily tasks. Training should be tailored to specific roles and responsibilities, and ongoing support should be provided to address user questions and issues. A lack of user adoption can undermine the entire implementation. Make sure to dedicate sufficient resources to training and change management.
Integration with Existing Systems
Most companies have other systems in place, such as CRM, SCM, or MES, that need to be integrated with the ERP system. Integration ensures that data flows seamlessly between systems and eliminates the need for manual data entry. Integration can be complex, so it’s important to carefully plan and test the integration process. Look for ERP systems with pre-built integrations or APIs that facilitate integration with other systems.
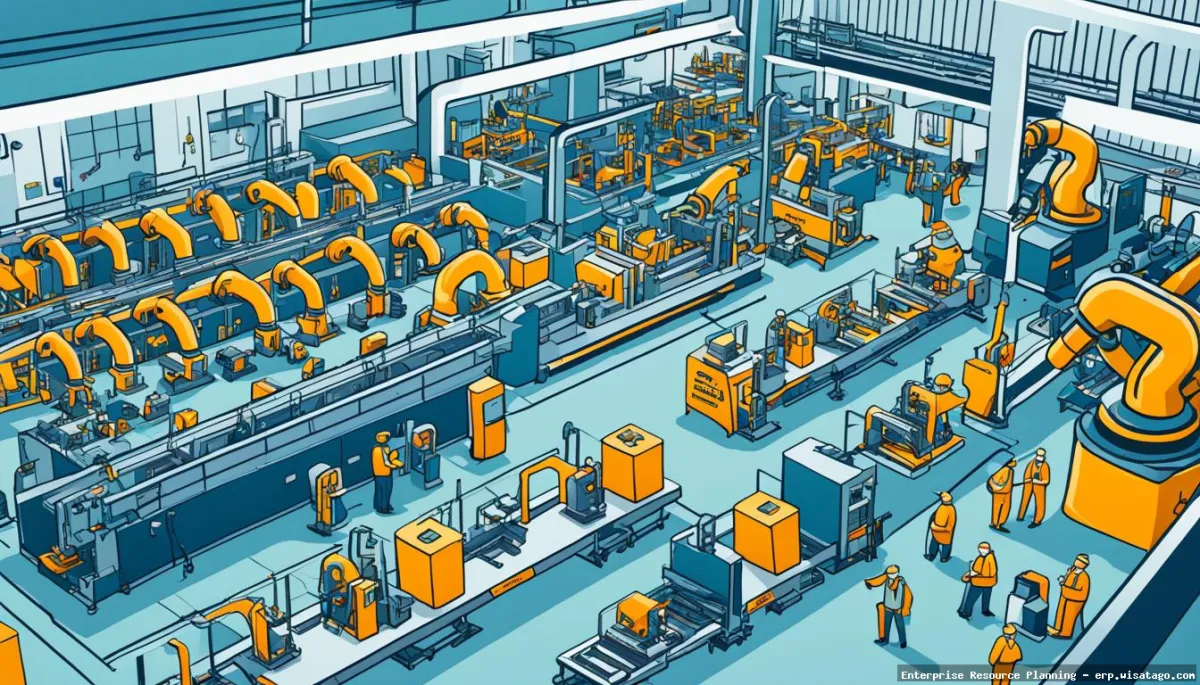
Choosing the Right ERP System
Selecting the right ERP system is crucial for a successful implementation. Consider the following factors when evaluating ERP systems:
- Industry-Specific Functionality: Does the system offer features and capabilities tailored to your specific industry?
- Scalability: Can the system scale to meet your future needs as your business grows?
- Ease of Use: Is the system user-friendly and intuitive to learn and use?
- Integration Capabilities: Does the system integrate easily with your existing systems?
- Vendor Reputation and Support: Does the vendor have a good reputation and provide reliable support?
- Cost: What is the total cost of ownership, including software licenses, implementation services, and ongoing maintenance?
Future Trends in MRP and ERP
The future of MRP and ERP is being shaped by several emerging trends:. For businesses seeking streamlined operations and enhanced decision-making capabilities, Advanced Erp Solutions offer a pathway to improved efficiency and productivity
Cloud-Based ERP
Cloud-based ERP systems are becoming increasingly popular due to their lower upfront costs, scalability, and ease of deployment. Cloud ERP allows companies to access the system from anywhere with an internet connection, and the vendor handles the maintenance and upgrades. This reduces the burden on internal IT resources and allows companies to focus on their core business.
Artificial Intelligence (AI) and Machine Learning (ML)
AI and ML are being integrated into ERP systems to automate tasks, improve decision-making, and enhance forecasting accuracy. AI-powered features can analyze data to identify patterns, predict demand, and optimize production schedules. ML algorithms can learn from historical data to improve the accuracy of forecasts and recommendations.
Internet of Things (IoT)
IoT devices are being used to collect real-time data from the shop floor, providing valuable insights into production processes. This data can be used to optimize production schedules, improve equipment maintenance, and reduce downtime. IoT integration allows for a more proactive and data-driven approach to manufacturing management.

Mobile ERP
Mobile ERP allows users to access the system from their smartphones or tablets, providing real-time information and enabling them to perform tasks remotely. This is particularly useful for sales representatives, field service technicians, and shop floor supervisors. Mobile ERP enhances productivity and improves responsiveness. Many businesses find that managing resources becomes increasingly complex, ERP offering a centralized platform to streamline operations and improve visibility
.
In conclusion, Manufacturing Resource Planning (MRP) is a critical component of modern ERP systems, enabling manufacturers to optimize their operations, reduce costs, and improve efficiency. By understanding the core functionalities of MRP, the benefits of integrating it with ERP, and the key considerations for implementation, companies can unlock the full potential of this powerful technology and achieve a competitive advantage in today’s dynamic manufacturing landscape.
Conclusion
In conclusion, modern ERP systems have revolutionized Manufacturing Resource Planning, moving far beyond the limitations of traditional MRP. By integrating data across all facets of the manufacturing process, from demand forecasting and inventory management to production scheduling and quality control, these sophisticated systems empower businesses to achieve unprecedented levels of efficiency, agility, and profitability. The ability to leverage real-time insights, automate critical processes, and optimize resource allocation is no longer a luxury, but a necessity for manufacturers seeking to thrive in today’s competitive landscape.
As we’ve explored, the successful implementation of MRP within a modern ERP hinges on careful planning, a deep understanding of business needs, and a commitment to continuous improvement. The benefits, however, are undeniable. If your organization is ready to unlock its full manufacturing potential and gain a significant competitive advantage, we encourage you to explore the possibilities of modern ERP solutions and consider how they can transform your operations. Investing in the right ERP system is an investment in your future. Learn more about optimizing your manufacturing processes by scheduling a consultation with our ERP experts today!
Frequently Asked Questions (FAQ) about Manufacturing Resource Planning in Modern ERP
How does a modern ERP system enhance Manufacturing Resource Planning (MRP) compared to standalone MRP systems, and what are the key benefits for manufacturers?
Modern ERP systems significantly enhance Manufacturing Resource Planning (MRP) by integrating it with other crucial business functions like finance, supply chain management, customer relationship management (CRM), and human resources. Standalone MRP systems typically focus solely on production planning and inventory control. The key benefits of an integrated ERP approach include improved data visibility across the entire organization, leading to better-informed decisions. This holistic view allows for more accurate demand forecasting, optimized inventory levels, reduced lead times, and enhanced production scheduling. Furthermore, modern ERP systems often incorporate advanced analytics and reporting capabilities, providing manufacturers with actionable insights to drive efficiency and profitability. The seamless flow of information eliminates data silos and streamlines processes, ultimately leading to a more agile and responsive manufacturing operation. For example, real-time sales data can directly influence production schedules, minimizing excess inventory and ensuring timely order fulfillment.
What specific MRP functionalities are crucial within a modern ERP system for effectively managing complex manufacturing processes, such as those involving custom configurations or engineer-to-order products?
For managing complex manufacturing processes, several MRP functionalities within a modern ERP system are critical. Bill of Materials (BOM) management that supports multi-level BOMs and engineering change orders is essential for custom configurations. Advanced planning and scheduling (APS) capabilities allow for optimized resource allocation and production sequencing, considering constraints like machine capacity and material availability. Work order management provides granular control over production processes, tracking costs and progress at each stage. For engineer-to-order (ETO) products, configuration management and product configurators are vital, enabling accurate quoting and order entry based on customer-specific requirements. Furthermore, robust data analytics and reporting tools provide insights into production performance, allowing for continuous improvement and optimization of complex manufacturing workflows. Integration with product lifecycle management (PLM) systems further streamlines the ETO process by ensuring that engineering designs are seamlessly integrated into the manufacturing process. These functionalities, working in concert, enable manufacturers to efficiently handle complexity and deliver customized products on time and within budget.
What are the key considerations when selecting and implementing a modern ERP system with MRP capabilities to ensure successful digital transformation in a manufacturing environment, and how can potential challenges be mitigated?
Selecting and implementing a modern ERP system with MRP requires careful consideration. Firstly, clearly define your business requirements and objectives for digital transformation. Assess your current manufacturing processes and identify areas for improvement. Secondly, choose an ERP system that aligns with your specific industry and manufacturing model (e.g., discrete, process, or mixed-mode). Consider factors like scalability, integration capabilities, and user-friendliness. Thirdly, plan for a phased implementation approach, starting with core MRP functionalities and gradually expanding to other modules. Data migration and user training are critical; allocate sufficient resources for these activities. Potential challenges like resistance to change, data quality issues, and integration complexities can be mitigated through strong leadership, clear communication, and a well-defined project management plan. Engage key stakeholders from all departments throughout the implementation process. Regular testing and validation are essential to ensure data accuracy and system functionality. Finally, prioritize ongoing support and maintenance to ensure the long-term success of your ERP investment. Consider a cloud-based ERP solution for increased flexibility and reduced IT infrastructure costs.