Warehouse Management Optimization Through ERP: Complete Guide, Features and Details
Warehouse management can often feel like a juggling act. You’re constantly trying to balance inventory levels, fulfill orders quickly, minimize errors, and keep costs down. For many businesses, especially those experiencing growth, spreadsheets and manual processes simply can’t keep up. That’s where Enterprise Resource Planning (ERP) systems come into play, offering a powerful solution to streamline and optimize warehouse operations.
I’ve seen firsthand how ERP can transform a chaotic warehouse into a well-oiled machine. I’ve been involved in multiple ERP implementations across different industries, from manufacturing to distribution, and the impact on warehouse efficiency is consistently significant. However, choosing and implementing the right ERP isn’t a walk in the park. It requires careful planning, a deep understanding of your business needs, and a commitment to change management. This guide aims to provide you with a comprehensive overview of how ERP can optimize your warehouse management, covering key features, implementation considerations, and best practices.
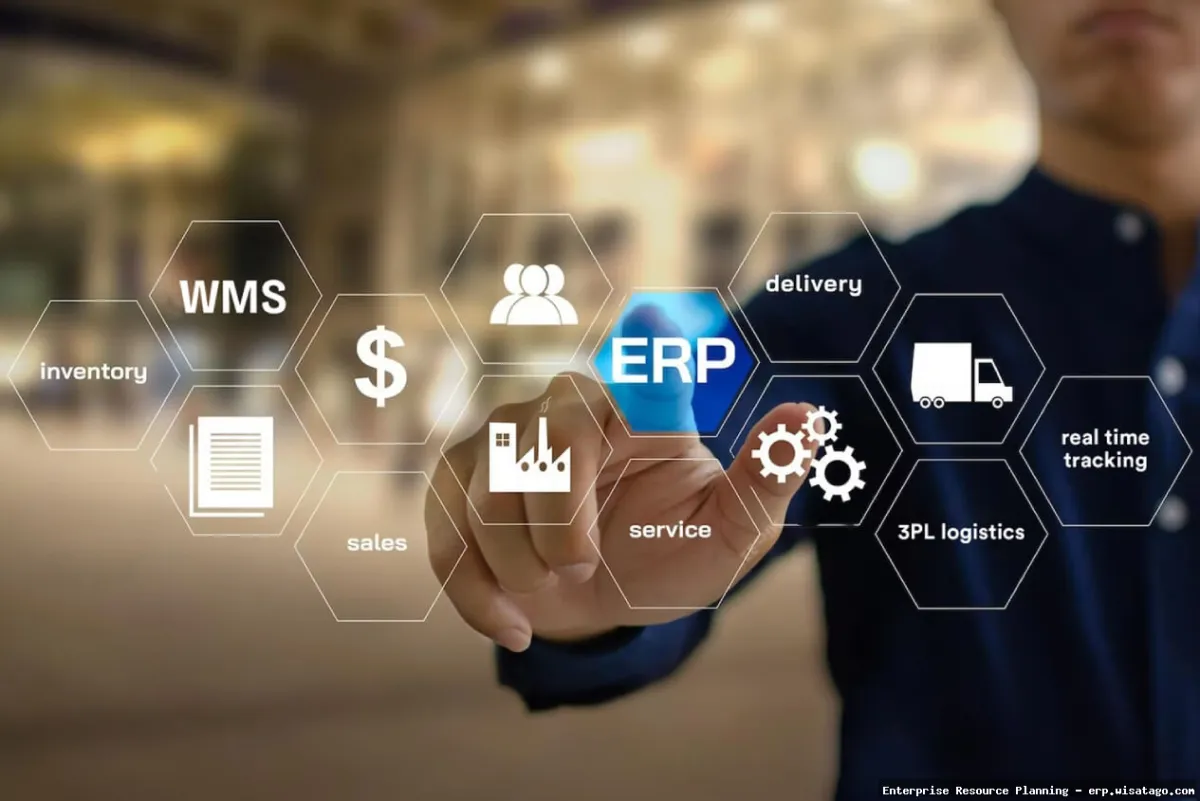
Think of ERP as the central nervous system of your business. It integrates all your core processes, including finance, human resources, supply chain management, and, of course, warehouse management. By connecting these functions, ERP provides a single source of truth for your data, eliminating silos and enabling better decision-making. In the context of warehouse management, this means real-time visibility into inventory levels, streamlined order fulfillment, and improved operational efficiency. Let’s dive into the specifics of how ERP achieves this.
Understanding the Core of ERP in Warehouse Management
At its core, ERP for warehouse management is about integrating all aspects of warehouse operations into a single, unified system. This integration allows for real-time visibility into inventory, improved accuracy in order fulfillment, and overall increased efficiency. It moves beyond basic inventory tracking to encompass everything from receiving and putaway to picking, packing, and shipping.
Key Benefits of ERP in Warehouse Management
Implementing an ERP system offers a wide range of benefits for warehouse management, including:
- Improved Inventory Accuracy: Real-time tracking of inventory levels reduces stockouts and overstocking, minimizing waste and improving customer satisfaction.
- Streamlined Order Fulfillment: Automated order processing and picking routes optimize the fulfillment process, leading to faster delivery times and reduced errors.
- Enhanced Visibility: Gain a comprehensive view of warehouse operations, from receiving to shipping, allowing for better decision-making and problem-solving.
- Reduced Labor Costs: Automation of tasks such as inventory counting and order processing reduces the need for manual labor, leading to cost savings.
- Improved Customer Service: Faster order fulfillment and accurate inventory information lead to happier customers and increased loyalty.
- Better Compliance: ERP systems help ensure compliance with industry regulations and standards, reducing the risk of penalties and fines.
Essential ERP Features for Warehouse Optimization
Not all ERP systems are created equal. When choosing an ERP for warehouse management, it’s crucial to consider the specific features that will best address your business needs. Here are some essential features to look for:
Inventory Management
This is the cornerstone of any good warehouse management system. Key features include:
- Real-time Inventory Tracking: Provides up-to-the-minute information on inventory levels, locations, and movements.
- Serial Number and Lot Tracking: Enables traceability of individual items or batches, essential for industries with strict regulatory requirements.
- Inventory Valuation: Supports various inventory valuation methods, such as FIFO, LIFO, and weighted average.
- Cycle Counting: Allows for regular inventory counts to identify and correct discrepancies.
- Min/Max Inventory Levels: Automatically triggers reordering when inventory levels fall below a certain threshold.
Warehouse Layout and Design
The system should allow you to map out your warehouse layout for efficient storage and retrieval.
- Storage Location Management: Defines and manages different storage locations, such as shelves, bins, and pallets.
- Slotting Optimization: Optimizes the placement of items within the warehouse to minimize travel time and improve picking efficiency.
- Warehouse Mapping: Creates a visual representation of the warehouse layout, making it easier to locate items.
Order Management and Fulfillment
Streamlines the entire order fulfillment process, from order entry to shipping.
- Order Processing: Automates the processing of customer orders, reducing manual data entry and errors.
- Picking and Packing: Supports various picking methods, such as batch picking, wave picking, and zone picking.
- Shipping Management: Integrates with shipping carriers to automate the shipping process and generate shipping labels.
- Returns Management: Manages the return of goods, including inspection, restocking, and refunds.
Receiving and Putaway
Efficiently manages the receiving and putaway of incoming goods.
- Receiving Management: Automates the receiving process, including inspection, verification, and data entry.
- Putaway Optimization: Optimizes the placement of incoming goods within the warehouse to minimize travel time and improve storage efficiency.
- Cross-Docking: Enables the direct transfer of goods from receiving to shipping, bypassing storage.
Reporting and Analytics
Provides insights into warehouse performance and identifies areas for improvement.
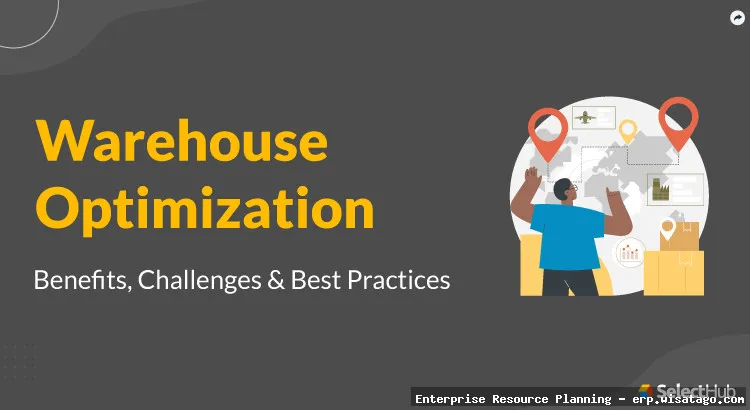
- Key Performance Indicators (KPIs): Tracks key metrics such as order fulfillment rate, inventory turnover, and warehouse utilization.
- Real-time Dashboards: Provides a visual representation of warehouse performance, allowing for quick identification of issues.
- Customizable Reports: Allows users to create custom reports to analyze specific aspects of warehouse operations.
Implementing ERP for Warehouse Management: A Step-by-Step Guide
Implementing an ERP system is a significant undertaking, but with careful planning and execution, it can deliver substantial benefits. Here’s a step-by-step guide to help you through the process:
1. Define Your Needs and Objectives
Start by clearly defining your business needs and objectives. What are the specific challenges you’re facing in your warehouse management? What improvements are you hoping to achieve with an ERP system? Involve key stakeholders from different departments in this process to ensure that all perspectives are considered.
2. Research and Select the Right ERP System
Once you have a clear understanding of your needs, it’s time to research and evaluate different ERP systems. Consider factors such as functionality, cost, scalability, and vendor reputation. Look for an ERP system that is specifically designed for warehouse management and that integrates well with your existing systems.
3. Plan Your Implementation
Develop a detailed implementation plan that outlines the scope of the project, the timeline, the resources required, and the roles and responsibilities of each team member. This plan should also include a detailed data migration strategy.
4. Configure and Customize the ERP System
Configure the ERP system to meet your specific business requirements. This may involve customizing the system to support your unique processes and workflows. Work closely with the ERP vendor to ensure that the system is properly configured and customized.
5. Train Your Users
Provide comprehensive training to all users of the ERP system. This training should cover all aspects of the system, from basic navigation to advanced functionality. Ensure that users understand how to use the system to perform their daily tasks. Investing in technology is crucial for sustained growth, with Advanced Erp Solutions enabling businesses to streamline operations and gain a competitive edge
6. Go Live and Monitor Performance
Once the system is configured and users are trained, it’s time to go live. Monitor the system closely to ensure that it is performing as expected. Identify and address any issues that arise promptly.
7. Continuously Improve
ERP implementation isn’t a one-time event. Continuously monitor the system’s performance and identify areas for improvement. Regularly review your processes and workflows and make adjustments as needed to optimize your warehouse operations.
Common Challenges and How to Overcome Them
ERP implementations aren’t always smooth sailing. Here are some common challenges and how to overcome them:
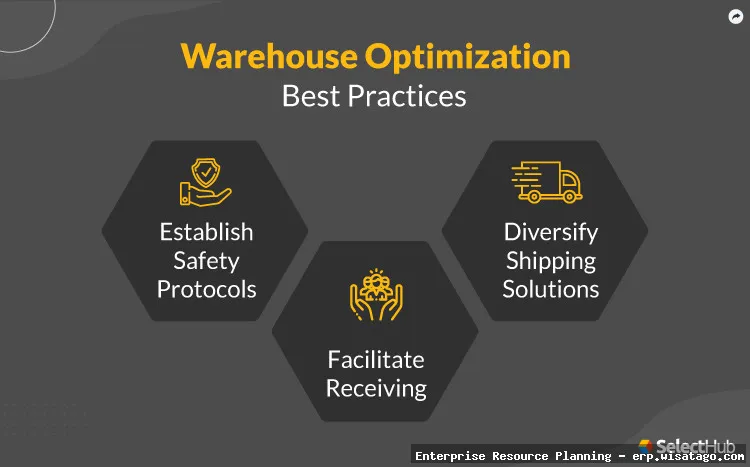
Data Migration
Migrating data from legacy systems to the new ERP system can be a complex and time-consuming process. To minimize the risk of errors, develop a detailed data migration plan and thoroughly validate the data after migration.
User Adoption
Getting users to adopt the new ERP system can be challenging, especially if they are accustomed to working with legacy systems. To encourage user adoption, provide comprehensive training, involve users in the implementation process, and communicate the benefits of the new system clearly.
Change Management
Implementing an ERP system requires significant changes to business processes and workflows. To manage these changes effectively, develop a comprehensive change management plan that includes communication, training, and support.
Integration with Existing Systems
Integrating the ERP system with existing systems can be complex, especially if those systems are outdated or poorly documented. To minimize integration challenges, choose an ERP system that offers robust integration capabilities and work closely with the ERP vendor to ensure that the integration is properly implemented.
Choosing the Right ERP Solution: Key Considerations
Selecting the right ERP solution is crucial for the success of your warehouse management optimization project. Here are some key considerations to keep in mind:. Many companies seek ways to improve efficiency, ERP becoming a frequently considered solution for integrated management
.
- Functionality: Does the ERP system offer the functionality you need to manage your warehouse operations effectively?
- Scalability: Can the ERP system scale to meet your growing business needs?
- Integration: Does the ERP system integrate well with your existing systems?
- Cost: Is the ERP system affordable and within your budget? Consider both the initial cost and the ongoing maintenance costs.
- Vendor Reputation: Does the ERP vendor have a good reputation for providing reliable and effective solutions?
- Industry Specificity: Does the ERP cater to your specific industry needs and regulations?
- Mobile Capabilities: Does the ERP offer mobile capabilities for warehouse workers to manage tasks on the go?
The Future of ERP in Warehouse Management
The future of ERP in warehouse management is bright, with advancements in technology driving even greater efficiency and automation. Here are some key trends to watch:
- Cloud-Based ERP: Cloud-based ERP systems offer greater flexibility, scalability, and affordability compared to on-premise systems.
- Artificial Intelligence (AI): AI is being used to optimize warehouse operations, such as predicting demand, optimizing picking routes, and automating inventory management.
- Internet of Things (IoT): IoT devices, such as sensors and RFID tags, are being used to track inventory in real-time and improve warehouse visibility.
- Robotics and Automation: Robots and automation are being used to automate tasks such as picking, packing, and shipping, reducing labor costs and improving efficiency.
By embracing these technologies, businesses can further optimize their warehouse operations and gain a competitive advantage.
Conclusion
Implementing an ERP system for warehouse management is a significant investment, but it can deliver substantial benefits in terms of improved efficiency, reduced costs, and increased customer satisfaction. By carefully planning your implementation, choosing the right ERP solution, and addressing common challenges proactively, you can transform your warehouse into a well-oiled machine. Remember to focus on user adoption, continuous improvement, and staying up-to-date with the latest technologies to maximize the value of your ERP investment. The journey to warehouse optimization through ERP is an ongoing process, but the rewards are well worth the effort.
Conclusion
In conclusion, the optimization of warehouse management through the implementation of an Enterprise Resource Planning (ERP) system presents a significant opportunity for businesses to enhance efficiency, reduce costs, and improve overall operational performance. By integrating key warehouse functions like inventory management, order fulfillment, and shipping, ERP systems provide a centralized platform for real-time visibility, streamlined processes, and data-driven decision-making. The benefits, as discussed, extend beyond simple automation, fostering a more agile and responsive supply chain capable of meeting the ever-evolving demands of today’s competitive market.
The journey towards warehouse management optimization with ERP requires careful planning, strategic implementation, and a commitment to continuous improvement. By embracing the power of integrated technology and leveraging the insights gained from data analytics, companies can unlock significant value and gain a competitive edge. If you’re ready to transform your warehouse operations and unlock the full potential of your supply chain, we encourage you to explore the ERP solutions available and consider how they can be tailored to meet your specific business needs. Learn more about how an ERP can transform your business here.
Frequently Asked Questions (FAQ) about Warehouse Management Optimization through ERP
How can implementing an ERP system specifically help to reduce picking and packing errors in my warehouse?
Implementing an ERP system can significantly reduce picking and packing errors in a warehouse through several key mechanisms. First, ERP provides real-time inventory visibility, ensuring that warehouse staff have accurate information on product availability and location. This minimizes the chances of picking the wrong item or quantity. Second, the system can enforce standardized processes for picking and packing, often incorporating barcode scanning or RFID technology to verify each item against the order. This validation step helps to catch errors before they escalate. Furthermore, ERP systems often include features like pick-to-light or voice-directed picking, which guide workers to the correct locations and items, thereby streamlining the process and reducing human error. Finally, data analysis within the ERP allows for identifying error patterns and implementing corrective actions, leading to continuous improvement in warehouse operations.
What are the key benefits of using an ERP system to improve inventory management within a warehouse environment, and how does it differ from using a standalone Warehouse Management System (WMS)?
An ERP system offers several key benefits for warehouse inventory management. It provides real-time visibility across the entire supply chain, integrating inventory data with other business functions like sales, purchasing, and finance. This holistic view enables better demand forecasting, optimized stock levels, and reduced carrying costs. ERP also facilitates automated inventory tracking, streamlining processes like receiving, put-away, and cycle counting, leading to increased accuracy and efficiency. While a standalone Warehouse Management System (WMS) focuses primarily on optimizing warehouse-specific tasks, an ERP system offers a broader scope, connecting the warehouse to the rest of the organization. A WMS excels at detailed warehouse operations like task interleaving and yard management, but it may lack the comprehensive integration capabilities of an ERP, which links warehouse activities to overall business strategy and financial performance.
How much does it typically cost to implement an ERP system for warehouse management optimization, and what are the factors that influence the overall implementation price?
The cost of implementing an ERP system for warehouse management optimization can vary significantly, ranging from tens of thousands to hundreds of thousands of dollars or more. Several factors influence the overall price. The size and complexity of the warehouse operation are primary drivers; larger warehouses with more complex workflows typically require a more extensive and customized ERP solution. The chosen ERP vendor and the specific modules selected also impact the cost. Cloud-based ERP systems often have lower upfront costs but recurring subscription fees, while on-premise solutions require investments in hardware and IT infrastructure. Customization requirements also play a role; the more customization needed to tailor the ERP to unique business processes, the higher the implementation cost. Finally, implementation services, including consulting, training, and data migration, contribute significantly to the total expense.